Analyzing real-world cases of fabrication-related risks
Analyzing real-world cases of fabrication-related risks provides valuable insights into the challenges and consequences that can arise during the fabrication phase of projects, particularly in industries like oil and gas, construction, and manufacturing. Here are two illustrative examples:
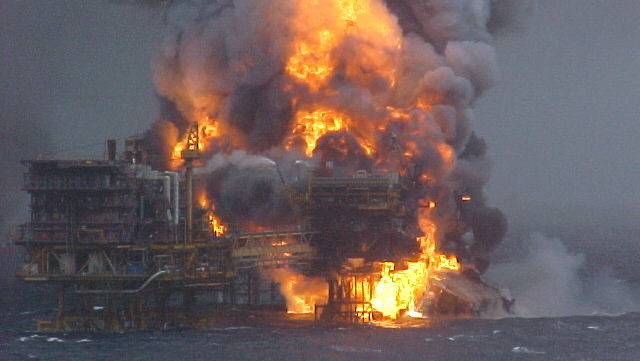
1. Piper Alpha Oil Platform Explosion (1988):
- Background: The Piper Alpha platform was an offshore oil production platform in the North Sea. On July 6, 1988, a catastrophic explosion and subsequent fires occurred on the platform, leading to the loss of 167 lives and the platform’s destruction.
- Fabrication-Related Risk: The disaster was rooted in a fabrication-related risk, as it was caused by the failure of a condensate pump’s pressure safety valve. The valve had been removed for maintenance, but the wrong gasket was used during reinstallation. This led to a gas leak, followed by the explosion.
- Consequences: The Piper Alpha disaster remains one of the deadliest offshore oil platform accidents in history. It not only resulted in significant loss of life but also caused extensive damage to the platform, disruption of oil production, and environmental damage due to oil spills and gas releases.
- Lessons Learned: The Piper Alpha disaster highlighted the critical importance of proper maintenance procedures, documentation, and the need for rigorous quality control during fabrication and maintenance activities. It also led to significant changes in offshore safety regulations and practices.
2. Space Shuttle Challenger Disaster (1986):
- Background: The Space Shuttle Challenger disaster occurred on January 28, 1986, when the NASA Space Shuttle Challenger disintegrated 73 seconds after liftoff, resulting in the loss of all seven crew members.
- Fabrication-Related Risk: While the direct cause of the disaster was the failure of an O-ring seal in one of the solid rocket boosters, this failure was rooted in a fabrication-related risk. The O-ring had lost its elasticity due to low temperatures at the time of launch, a condition exacerbated by the design of the booster joints.
- Consequences: The Challenger disaster had profound consequences not only in terms of human loss but also for the space program and NASA’s reputation. It led to a suspension of the Space Shuttle program, significant redesigns of the shuttle boosters, and a reevaluation of safety protocols.
- Lessons Learned: The Challenger disaster underscored the need for rigorous quality control, thorough testing, and attention to detail in the fabrication and design of critical components, particularly in high-risk environments like space exploration.
In both of these real-world cases, fabrication-related risks had devastating consequences. They highlight the importance of quality control, adherence to safety protocols, rigorous maintenance procedures, and continuous risk assessment throughout the lifecycle of assets or projects. These lessons have had a lasting impact on the respective industries, emphasizing the need for proactive risk management and a commitment to safety and integrity in all fabrication-related activities.