Identifying and mitigating safety hazards
Identifying and mitigating safety hazards is a crucial aspect of ensuring the well-being of workers and the smooth operation of any fabrication process. Below are steps to help identify and address safety hazards effectively:
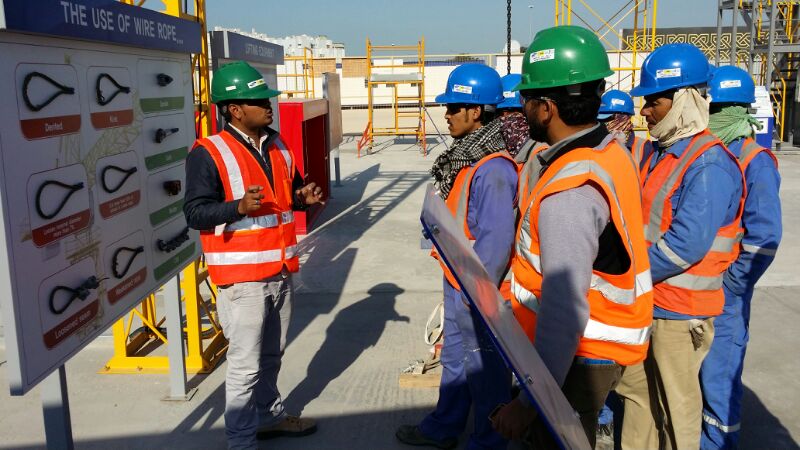
1. Conduct a Hazard Assessment:
- Regularly assess the fabrication facility for potential hazards. This can be done through safety inspections, risk assessments, and job hazard analyses.
2. Involve Workers:
- Workers who are actively engaged in fabrication processes often have valuable insights into potential hazards. Encourage them to report safety concerns and involve them in hazard identification and mitigation efforts.
3. Review Incident Reports:
- Analyze past incident reports and near misses to identify recurring safety issues. Use this information to address root causes and prevent future occurrences.
4. Use Safety Data Sheets (SDS):
- Ensure that Safety Data Sheets are readily available for all chemicals and hazardous materials used in the facility. Train workers to understand SDS and follow safety protocols for handling and storage.
5. Prioritize Hazards:
- Prioritize identified hazards based on their severity and likelihood of occurrence. Focus on addressing high-risk hazards first.
6. Implement Engineering Controls:
- Whenever possible, use engineering controls to eliminate or reduce hazards. This may involve modifying equipment, adding safety features, or implementing safer processes.
7. Provide Personal Protective Equipment (PPE):
- Ensure that workers have access to and are trained in the proper use of PPE, such as safety glasses, hearing protection, gloves, helmets, and respiratory protection, as needed.
8. Establish Standard Operating Procedures (SOPs):
- Develop and implement written SOPs for all fabrication processes. These procedures should outline safe work practices, including equipment setup, operation, maintenance, and shutdown.
9. Conduct Training:
- Train all employees, including new hires, on safety protocols, hazard recognition, and emergency procedures. Provide refresher training regularly.
10. Promote Good Housekeeping:
- Maintain a clean and organized workspace to reduce tripping hazards, prevent material spills, and facilitate emergency response.
11. Control Dust and Fumes:
- Implement effective dust and fume control measures, including local exhaust ventilation systems, to minimize respiratory hazards.
12. Ensure Proper Machine Guarding:
- Machines and equipment should have proper guarding to prevent accidental contact with moving parts. Conduct regular inspections to ensure guards are in place and functioning correctly.
13. Manage Chemicals Safely:
- Label and store chemicals properly, provide appropriate ventilation in chemical storage areas, and ensure that workers are trained in chemical handling and emergency response.
14. Address Ergonomic Concerns:
- Identify and address ergonomic hazards by providing ergonomically designed tools and workstations and training workers on proper ergonomic practices.
15. Establish Emergency Procedures:
- Develop and communicate emergency response procedures, including evacuation plans, first-aid stations, and reporting mechanisms for accidents and incidents.
16. Monitor and Review:
- Continuously monitor the workplace for changes in hazards and review safety measures to ensure they remain effective. Encourage worker feedback on safety improvements.
17. Conduct Safety Drills:
- Regularly practice emergency drills, such as fire drills or confined space rescues, to ensure that workers are prepared to respond effectively in case of an emergency.
18. Compliance with Regulations:
- Stay up-to-date with local, state, and federal regulations and ensure that your facility complies with all applicable safety standards.
19. Reporting and Investigation:
- Establish a process for reporting and investigating safety incidents, near misses, and hazards. Use this information to make improvements.
20. Safety Culture:
- Foster a strong safety culture where all employees prioritize safety, report hazards, and actively participate in safety initiatives.
By consistently following these steps and involving workers in safety efforts, fabrication facilities can create a safer work environment and reduce the risk of accidents and injuries. Regular safety audits and ongoing training are critical for maintaining a strong safety program.