Exploration of AIM throughout the asset’s lifecycle
Lesson 1.2: AIM Lifecycle Phases
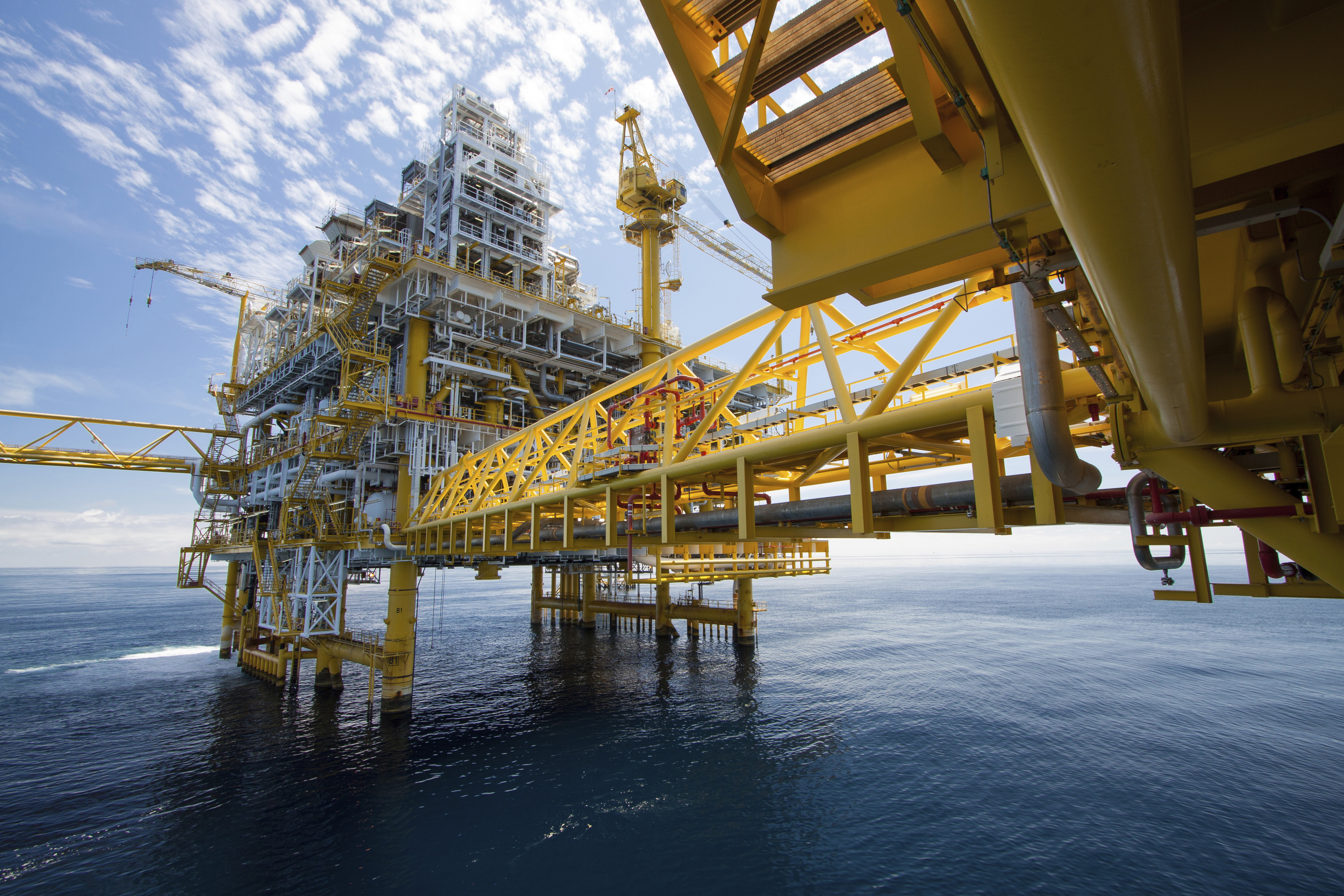
Asset Integrity Management (AIM) is a comprehensive and continuous process that extends throughout the entire lifecycle of an asset in industries such as oil and gas, petrochemicals, and power generation. The AIM framework ensures the safety, reliability, and efficiency of critical infrastructure from design and construction through operation and maintenance to decommissioning. Let’s explore how AIM is applied at each stage of an asset’s lifecycle:
1. Design and Engineering Phase:
AIM Integration: AIM principles are embedded in the initial design and engineering phases. Asset integrity considerations are integrated into the design process to ensure that the asset is inherently safe, reliable, and maintainable.
Risk Assessment: During design, a risk assessment is conducted to identify potential integrity risks associated with the asset’s design, location, and intended operation. This informs design decisions and risk mitigation strategies.
Materials Selection: AIM influences the selection of materials and construction methods to withstand the operational environment, such as corrosion-resistant materials for offshore structures or high-temperature alloys for refining equipment.
Regulatory Compliance: Design must comply with industry regulations and standards. AIM managers work closely with designers to ensure that these standards are met.
2. Construction and Fabrication Phase:
Quality Control: AIM managers oversee the construction process to ensure that quality control measures are in place. This includes welding inspections, material traceability, and adherence to design specifications.
Safety Procedures: Safety protocols and practices are enforced during construction to protect workers and the environment. AIM managers are responsible for ensuring that these procedures are followed.
Documentation: Comprehensive documentation of materials, construction processes, and inspections is essential for AIM. This documentation serves as a reference for future maintenance and inspections.
3. Commissioning Phase:
Testing and Inspection: AIM plays a vital role in commissioning by ensuring that all systems are tested and inspected thoroughly before the asset goes into full operation. This includes functional testing, pressure testing, and NDT inspections.
Data Collection: Data collected during commissioning is a valuable resource for future AIM activities. This data provides a baseline for asset performance and integrity.
Training: AIM managers ensure that operations and maintenance personnel are trained in the proper procedures for operating and maintaining the asset safely and efficiently.
4. Operation Phase:
Monitoring and Inspection: AIM involves continuous monitoring and inspection of the asset’s condition during its operational life. This includes real-time data from sensors and periodic inspections to identify potential integrity issues.
Preventive Maintenance: Scheduled maintenance and inspections are performed to address issues before they become critical. Preventive maintenance tasks are based on AIM data and analysis.
Safety and Environmental Compliance: AIM managers ensure that safety and environmental regulations are consistently met during operations. This includes regular safety audits and environmental impact assessments.
Data Analysis: Data collected from monitoring and inspections are analyzed to assess asset health and predict potential issues. Predictive maintenance strategies are employed to optimize maintenance efforts.
5. Decommissioning Phase:
Asset Integrity During Decommissioning: AIM extends to the decommissioning phase, where assets are safely and responsibly retired. AIM managers oversee the process to ensure that safety and environmental standards are maintained during decommissioning activities.
Data Preservation: Comprehensive records are preserved during decommissioning, including documentation of asset condition and any environmental remediation efforts. These records can inform future AIM activities if similar assets are replaced or repurposed.
Lessons Learned: AIM managers capture lessons learned during decommissioning to improve future design, construction, and operation of assets.
6. Continuous Improvement:
AIM Performance Review: Throughout the asset’s lifecycle, AIM managers conduct performance reviews to assess the effectiveness of AIM strategies and identify areas for improvement.
Benchmarking: AIM managers compare their AIM practices with industry best practices and performance benchmarks to drive continuous improvement.
Innovation: AIM embraces technological advancements, such as digital twins, predictive analytics, and remote monitoring, to enhance asset integrity and efficiency.