Fabrication Techniques and Processes
Fabrication techniques and processes are fundamental to various industries, including manufacturing, construction, aerospace, automotive, and more. These techniques involve shaping raw materials into finished products through various methods. Here’s an overview of common fabrication techniques and processes:
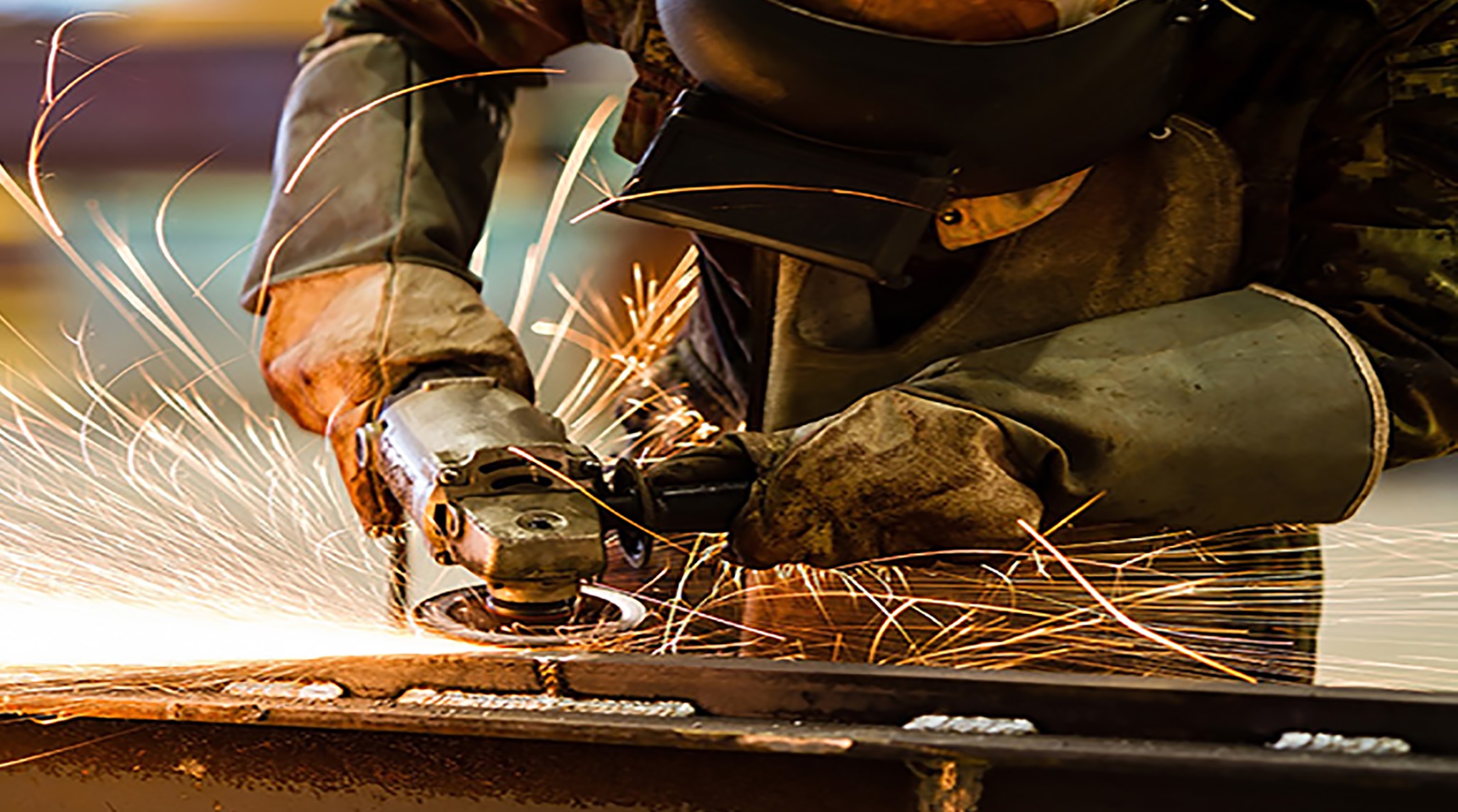
1. Cutting:
- Cutting Techniques: Cutting involves the removal of excess material to shape workpieces. Techniques include sawing, shearing, laser cutting, plasma cutting, waterjet cutting, and electrical discharge machining (EDM).
2. Joining:
- Welding: Welding fuses materials together by melting them at the joint. Common welding methods include arc welding, MIG (Metal Inert Gas) welding, TIG (Tungsten Inert Gas) welding, and spot welding.
- Brazing and Soldering: These methods join materials using a lower melting point filler material, called a solder or brazing rod, which bonds the parts together when melted.
- Adhesive Bonding: Adhesives and glues are used to bond materials together. This technique is particularly useful for joining dissimilar materials.
**3. Forming:
- Rolling: Rolling shapes materials into curved or cylindrical forms, commonly used in metalworking and the production of cylindrical objects like pipes and tubes.
- Pressing: Pressing or stamping uses a press machine to shape materials by applying force. It’s used in manufacturing sheet metal parts, coins, and more.
- Forging: Forging involves shaping materials by applying localized compressive forces. It’s widely used in the production of metal parts like automotive components and tools.
**4. Machining:
- Turning: Turning operations rotate a workpiece while a cutting tool removes material to create cylindrical shapes. Lathes are commonly used for turning.
- Milling: Milling machines use rotary cutters to remove material from a workpiece’s surface to create complex shapes and features.
- Drilling: Drilling creates holes in materials using rotating cutting tools. It’s essential in manufacturing and construction.
- Grinding: Grinding uses abrasive wheels to remove material and create precision surfaces and shapes. It’s used for finishing and precision work.
**5. Additive Manufacturing:
- 3D Printing: 3D printing builds objects layer by layer from digital models. It’s increasingly used for rapid prototyping and custom part production.
**6. Casting:
- Die Casting: Molten material is forced into a mold cavity to produce complex metal parts. It’s common in automotive and appliance manufacturing.
- Sand Casting: Sand casting uses sand molds to create metal parts. It’s versatile and used for a wide range of components.
- Investment Casting: This precision casting method produces detailed and intricate parts using wax or other materials as the mold.
**7. Extrusion:
- Plastic Extrusion: Plastic materials are forced through a die to create long, continuous shapes like pipes, tubes, and profiles.
- Aluminum Extrusion: Similar to plastic extrusion, but used for aluminum and other metals to create custom profiles and shapes.
**8. Heat Treatment:
- Annealing: Annealing is a heat treatment process that alters material properties, such as hardness and ductility, to make it easier to work with or improve its final properties.
**9. Surface Finishing:
- Painting and Coating: Surface finishing techniques like painting and coating protect materials and provide aesthetic finishes.
- Plating: Plating adds a layer of metal, such as chrome or nickel, to enhance corrosion resistance and appearance.
These fabrication techniques and processes are essential for creating a wide range of products across various industries. The choice of technique depends on factors like material type, desired product characteristics, production volume, and cost considerations. Advancements in technology and materials continue to drive innovations in fabrication processes, enabling the production of increasingly complex and precise components.